Die Bedeutung der Qualitätskontrolle, ihre Geschichte und ihre Phasen in der Draht- und Kabelindustrie
Eine der wichtigsten Stufen der Draht- und Kabelproduktion ist die Kontroll- und Qualitätsstufe sowie das Labor, das in jeder Fabrik vorhanden sein sollte. In diesem Stadium werden der elektrische Widerstand von Leiterdraht und Mantel, Zugfestigkeit, Kälte gemessen. Die Qualitätskontrolleinheit wurde eingerichtet, um Nacharbeitskosten zu sparen und Verschwendung zu vermeiden und die Ziele der Organisation / Unternehmensqualitätspolitik zu erreichen sowie die Kundenzufriedenheit gemäß ISO 9001-Standard sicherzustellen.
Jedes Unternehmen mit einer Qualitätskontrolleinheit mit erfahrenen Mitarbeitern, die “in der Regel unter der direkten Aufsicht des CEO operiert”, hat in der Bewertung unter anderen Herstellern eine hohe Punktzahl. Der Tätigkeitsbereich der Qualitätskontrolleinheit stimmt mit der Produktionseinheit überein und geht weit darüber hinaus. Eine Kontrolle von der Anfangsphase, also dem Einkauf der Rohstoffe, bis zur Endphase, der Präsentation des Produkts beim Kunden, ist notwendig. Die Kontrollschritte sind in drei allgemeine Abschnitte unterteilt: Kontrolle der Rohstoffe und Übereinstimmung ihrer Spezifikationen mit den Bedürfnissen des Unternehmens, Kontrolle während des Produktionsprozesses und Einhaltung von Standards.
Die abschließende Produktprüfung und Vorlage des Kontrollblatt-Prüfblattes mit allen relevanten Angaben erfolgt durch die Inspektoren der Qualitätskontrollstelle mit den Teilmengen Niederdrucklabor, Hochdrucklabor und Kalibrierstelle. Da Drähte und Kabel in Stromversorgungssystemen usw. ohne ein potenzielles Sicherheitsrisiko darstellen, sind Qualität und verbindliche Standards in der Draht- und Kabelindustrie wichtig. Man kann mit Sicherheit sagen, dass der empfindlichste und wichtigste Teil der Qualitätskontrolleinheit der Kalibrierungsabschnitt ist. Die Bestätigung der Messmittel erfolgt in Form eines vom Kalibrierunternehmen ausgestellten und an den jeweiligen Geräten angebrachten Etiketts, dessen Zertifikat ausgestellt und in der Gerätehistorie aufbewahrt wird.
Im Bezug auf Produkt -design, -produktion und -inspektion kommen statistiche Techniken zum Einsatz. Diese statistiche Qualitätskontrolle dient dazu, dass die Produktqualitätstandards erfüllt werden.
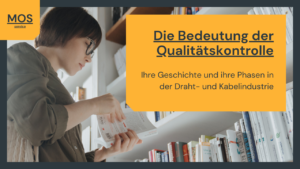
Jeder Kontrollprozess umfasst die folgenden Schritte:
1- Festlegung und Etablierung eines Standards, auf dessen Grundlage Funktionen bewertet werden.
2- Prüfung und Registrierung von Qualitätsmerkmalen zum Vergleich mit Standardkriterien
3- Analyse von Abweichungen und Nichtkonformitäten
4- Gestaltung und Durchführung von Korrekturmaßnahmen
In der Draht- und Kabelindustrie, da die kodifizierten und verbindlichen Normen der anwendbare Rahmen für die Festlegung der Normen für Qualitätsspezifikationen verschiedener Kabeltypen sind, ist die Verwendung von Standardbroschüren und zusätzlich die Verwendung internationaler Normen und Werksnormen zur Aufrechterhaltung der Produktqualität und Kontinuität während der gesamten Lebensdauer des Drahts oder Kabels entscheidend.
Die Qualitätskontrolle für Drähte und Kabel ist für die Qualitätssicherung der hergestellten Produkte in Bezug auf Qualität und Quantität verantwortlich. Aus diesem Grund sind gemäß dem Qualitätsmanagementsystem die Kontrollprozesse in drei Gruppen wie folgt:
– Kontrolle der eingehenden Artikel
– Inspektion während des Prozesses
– Inspektion des Endprodukts
Kontrolle der eingehenden Artikel
Alle Rohstoffe haben Einfluss auf die Qualität der kontrollierten Endprodukte, d.h. die technischen Spezifikationen für jeden Rohstoff werden nach den einschlägigen Normen festgelegt und sind zusammen mit den Kontrollbereichen und Akzeptanzkriterien im Technischen Datenblatt (MS) definiert. Die Handelseinheit kauft Rohstoffe aus der Liste der autorisierten Lieferanten nach der gleichen Ausführungsmethode und gibt sie nach Inspektion und Durchführung der erforderlichen Tests im Labor der Qualitätskontrolleinheit frei. Die im Lager freigegebenen Rohstoffe können als Rohstoffe in der Produktionseinheit verwendet werden.
Prüfung während der Bearbeitung
Gemäß der Durchführungsmethode der Qualitätskontrolle für jedes Gerät, für das ein Produktionsprozess definiert ist, werden Kontrollstationen in der Produktionsabteilung festgelegt und Kontrollparameter sowie die Anzahl der Bemusterungs- und Annahmekriterien bestimmt und in täglichen Qualitätskontrollformularen festgehalten. Erst wenn die Bewertungswerte jeder Produktspule übereinstimmen wird mit Zustimmung des Linienprüfers die Erlaubnis zur Verwendung im nächsten Prozess erteilt. Die täglich erfassten Ergebnisse der Qualitätskontrollstelle fließen in die kontinuierliche Verbesserung des Qualitätsmanagementsystems und in die statistischen Analysen monatlich und jährlich ein, um Verbesserungsmöglichkeiten zu schaffen.
Bei Nichteinhaltung während des Produktionsprozesses wird von der Qualitätskontrolle der Produktionsbetrieb der Auftrag zur Einstellung der Produktion erteilt und Korrekturmaßnahmen zur Beseitigung der Fälle eingeleitet.
Von jedem Endprodukt, einschließlich unbeschichteter, beschichteter Stromkabel und selbsttragender Luftleiter, wird ein Muster nach dem Zufallsprinzip hergestellt und zur Musterprüfung an das Qualitätskontrolllabor geschickt.
Bei der Endkontrolle werden zwei Prüfungen zur Messung des elektrischen Widerstands des Leiters und Spannungsprüfungen an 100 % der hergestellten Produkte durchgeführt. Bei Nichtkonformität des Endprodukts wird die Riemenscheibe von der Qualitätskontrolle in das Quarantänelager überführt und die Entscheidungs- und Korrekturmaßnahmen während des Nichtkonformitätskontrollformulars koordiniert.
Tag: Qualitätskontrolle Kreuzworträtsel , dissonanz , baubegleitende qualitätskontrolle, Die Bedeutung der Qualitätskontrolle, Qualitätssicherung in Frankfurt, Qualitätsmanagement in Frankfurt, Personaldienstleistung in Frankfurt, Industriedienstleistungen in Frankfurt, Bauteilmontage in Frankfurt, MOS Industrieservice GmbH Qualitätsmanagement in Frankfurt.